植物由来のセルロースファイバーで循環型モノづくりを加速
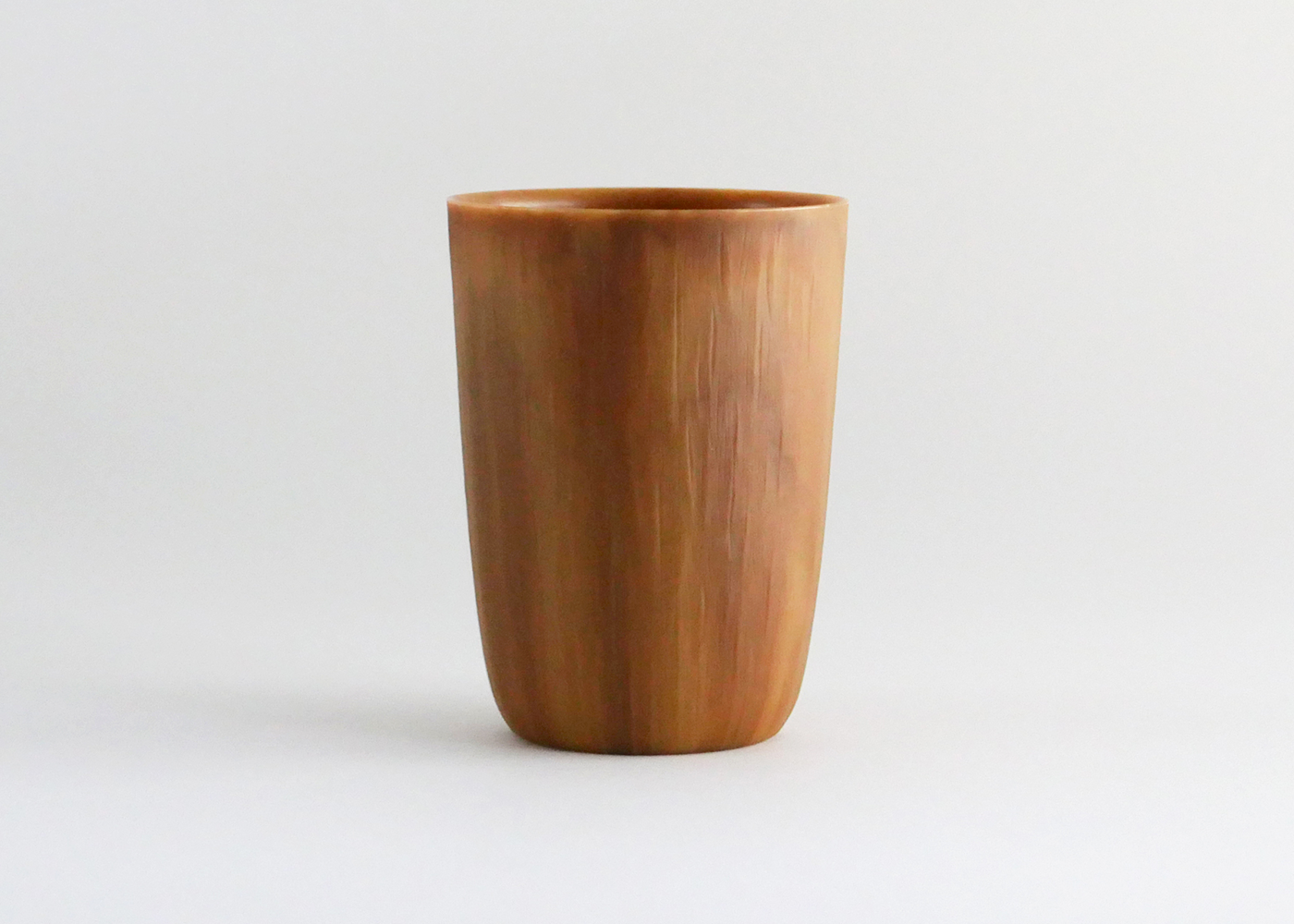
グローバルで300を超える事業場を持つパナソニック。モノづくりの現場で使用するプラスチックの量を減らし循環型社会の実現に貢献すべく、プラスチックの代替素材となるエコマテリアルの研究開発を進めています。
2019年には植物由来のセルロースファイバーを高濃度で樹脂に混ぜ込む複合加工技術を開発。循環型モノづくりを推進する成形材料として、家電筐体やリユースカップなどへの展開を進めています。
世界で消費されるプラスチックの量は年間3億トンを突破しており、更に増加の傾向にあります。一方で、リサイクルされるプラスチックはわずか14%と言われます(国際連合環境計画資料より)。海洋に捨てられるプラスチックごみ問題、石油資源の枯渇・地球温暖化などの環境問題もあり、石油由来のプラスチックの削減が世界的に求められています。国連が採択した「持続可能な開発目標(SDGs)」でも、「天然資源の効率的な利用」「海洋汚染の防止および大幅な削減」が目標として定められています。
こうした動きを受け、当社は2015年からエコマテリアルの研究開発をスタートしました。着目したのは植物由来成分であるセルロースファイバーです。これは植物の主成分であるセルロースから繊維を抽出して微細化し、補強用繊維として樹脂に混ぜ込んで作るもので、軽さ・強度を実現しながら環境にも配慮した成形材料になりうるバイオマス素材です。
セルロースファイバーの材料となるのは木材繊維(パルプ)。これは再生可能な天然資源である木から得ることができます。木材繊維は間伐材などの森林資源や産業廃棄物を含む植物資源からも取り出すことができ、計画的に植林などを行うことで再生産が可能な持続型の資源として注目されています。
従来の乾燥工程を無くした「全乾式プロセス」
セルロースファイバーは一般的にパルプを水中でほぐし、解繊する(繊維をより細かい状態にする)ことで製造されます。解繊したセルロースファイバーを樹脂と複合化する際には乾燥させる必要があり、そのエネルギーコストが課題となっていました。そこで当社は水を使用せず、溶解した樹脂の中でパルプを解繊しながら複合化する独自の「全乾式プロセス」を開発。乾燥工程をなくし、より効率的に製造できる仕組みを構築しました。
この全乾式プロセスによって実現したセルロースファイバー樹脂は、2018年8月発売の当社コードレススティック掃除機 MC-SBU820J/MC-SBU620Jの筐体に採用されました。本製品に採用されたセルロースファイバー樹脂ではガラス繊維の約8倍にもなる耐衝撃性を実現し、強度を確保すると同時に、プラスチック使用量の削減を両立しました。
さらに2019年に開発した複合加工技術では、樹脂にセルロースファイバーを55%の高濃度で混ぜ込めるようになりました。今後も強度や耐久性などの特性を高めつつ、さらなる品質改良を目指します。
リサイクルのしやすさも確保
セルロースファイバーには、処分やリサイクルのしやすさという特長もあります。グラスファイバー材料の場合は、使用後に燃やすとガラス繊維が残ってしまうため、埋め立てなどの処理が必要となります。また、リサイクルにまわせたとしても強度が低下してしまいます。一方、セルロースファイバー成形材料は植物繊維を採用しているため燃やしても何も残りません。また当社開発の近赤外線センサによる高精度樹脂選別システムにより樹脂の種類ごとに分別回収することができ、比較的強度を保った状態で再生材料として再利用することができます。
着色自由度の高いリユースカップを展開
当社のセルロースファイバー樹脂は、独自の混練(溶かし、混ぜ合わせ、均一化する)技術により、複合化の際に白色の成形材料として生成されます。このため成形の際の着色自由度が高くなり、植物原料の特徴に沿った独特の木質感、香りなども表現することができます。
2019年8月にはアサヒビール株式会社と共同で高濃度セルロースファイバー成形材料を活用したリユースカップを開発。屋外におけるイベントや店頭での持ち帰り用のビール類の提供を想定し、テスト展開を開始しています。
当社は2017年に「パナソニック環境ビジョン2050」を策定し、2050年に向けて、使うエネルギーの削減と、それを超えるエネルギーの創出・活用を目指していきます。今後もセルロースファイバー成形材料の利用拡大を推進していくと共に、「事業を通じた持続可能な社会への貢献」を目指して新しいエコマテリアルの開発にも挑戦してまいります。ご期待ください。
プレスリリース